Atomic force microscopy
Atomic force microscopy (AFM) is without doubts the most widespread technique from the family of microscopes with
scanning probe (SPM - Scanning Probe Microscopy). Method is based on detection of position of small probe which
is kept at close vicinity above the surface of the sample using a loopback. The probe is scanning the surface in regular
pattern.
There are different mechanisms of detection of the distance between the probe and the surface. In the case of AFM
there is detection of force between the probe and the surface. For the movement of probe above the surface typically
piezoceramic actuators are mostly used. These are able to achieve sub-nanometer resolution.
The most common method for detection of force between the probe and the surface is based on deformation
of flexible tip holder - the cantilever and detection of the deformation using laser beam and quadrant photodiode (principle
of optical lever). For the sensitivity of the method it is important the stiffness of the cantileveru should be as small as possible
which translates to 0.1 to 100 N/m in practice.
If we measured how the force depends on the distance between the probe and the surface we would notice attractive forces
(at larger distances there are electrostatic or van der Waals forces) and repulsive forces (at smaller distances, due to
electron clouds overlap.
At measurement using AFM we recognize several basic modes of scanning the surface depending if the tip and surface are in
attracting or repulsive region of force.
| 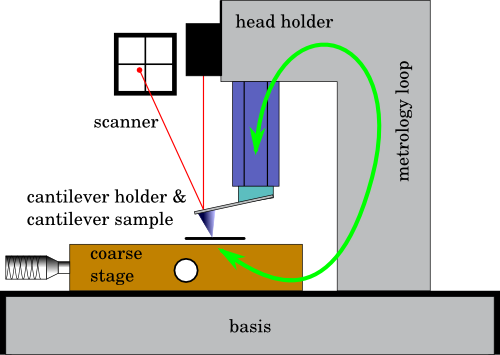 |
A commercial AFM schematics |
-
Cantilever deformation is kept at constant value, system tip-surface is in region of repulsive forces. This type is referred to as
contact mode.
- The tip is oscillating in z-axis at its resonant frequency (more precisely, at the resonant frequency of cantilever-tip couple).
Attractive force by which the surface acts on the tip results in shift of the resonant frequency towards lower values. The loopback
keeps the tip at such distance where the frequency shift or change of amplitude is constant. This type of control is mostly called
non-contact mode.
- The tip oscillates the same way as in previous case but reaches to region of repulsive forces. This type of control is called tapping
mode.
During the measurement the tip is typically rastering in regular pattern and gets information matrix representing
local height of surface and thus mapping the topography of sample. Acquired data must further be processed and analysed to calculate
the surface parameters we want to know. Except the tools usually included with the microscope we can conveniently do this using
free software Gwyddion [1].
Except the measurement of surface topology it is possible to realize more complicated experiments.
One of them is measurement of local mechanical response using dependence force-distance, which in
principle is a method usable for measurement of material hardness or adhesion between tip and the surface.
Such measurement can theoretically be realized in each point and map the mechanical properties of sample
in very high resolution.
Quantitative mesurement
Calibration of length measurement using a microscope is rather easy. For example, reference samples can be used as described in
general section about morphology measurement in nanometrology.
The principal characteristic artefact that we should take into account at data processing is the convolution of tip with the sample
which has an impact on dimension measurement but also on calculated statistical parameters such as roughness [2] or fractal properties.
If we decide to use the information about force acting between the tip and surface we have to calibrate the contilever stiffness
constant at first. To achieve this, several approaches can be used:
-
the use of cantilever geometry assuming we know the mechanical properties of material it is made of and
is necessary to precisely measure the dimensions. Even in such case the uncertainity of stiffness
is of the magnitude of tens of percent. The traceability is very problematic.
-
the use of thermal noise of cantilever, comparison to another cantilever, analysis using added mass and other indirect
methods described in literature. The uncertainity is near five percent, the traceability can be realized on at least some
of these methods.
- the use of nanoindentor as a force generator and displacement sensor. The uncertainity is about ten percent, the traceability
can be reached very easily.
At the use of the more complicated method (like local mechanical analysis using force modulation) it is always necessary to
decide how to calculate uncertainity and assess the influence of artifacts on the results.
[1] D. Nečas, P. Klapetek, Gwyddion: an open-source software for SPM data analysis, Central European Journal of Physics, 10 (2012) 181-188
[2] Petr Klapetek, Ivan Ohlídal: Theoretical analysis of the atomic force microscopy characterization of columnar thin films, Ultramicroscopy, 94, (19-29), Amsterdam, 2003
[3] Petr Klapetek, Ivan Ohlídal, Jindřich Bílek, Atomic force microscope tip influence on the fractal and multi-fractal analyses of the properties
of randomly rough surfaces Nanoscale Calibration Standards and Methods, ed. by G. Wilkening and L Koenders, Wiley VCH, p. 452, 2005
|