Mechanical properties
During the measurements of mechanical properties we are triyng to determine e.g. the indentation hardness, modulus of elasticity,
adhesion of a thin film to a substrate and similar quantities. These are the properties that have a fundamental influence on the application of the sample in the real world (e.g. the wear resistance) and therefore play the key role in the nanotechnology application into the industry.
At first sight the scanning probe microscopy methods such as Atomic Force Microscopy (AFM) seem to be the ideal tools for local mechanical properties measurements. This method is based on the evaluation of the force acting between the probe and the
surface and therefore it is easy to perform a measurement of the response of the sample on different forces applied by the probe. The problem is that
the AFM considering its construction is not by far the ideal force to other quantity (most often voltage) converter. Even though the principle of a deflection of a flexible probe holder by a force acting between the probe and the sample provides high sensitivity needed for nondestructive
morphology measurement, it lacks for small dynamic range and poor linearity which would be primarily expected from a device dedicated to the
measurement of mechanical properties.
On the other hand, the AFM is capable of performing measurements with high lateral resolution which is a property worth the
effort to quantitatively evaluate the force curves. It is equipped with different special regimes enabling the data acquisition representing the
hardness, elasticity modulus, adhesion and similar quantities with a minimal sample damage. The basic steps in the traceability of the force
and distance (between the probe and the surface) are the calibration of the spring constant of the probe holder (so called cantilever) and the
characterization of the probe diameter. Both of these factors have to be calibrated separately for each probe and in case of the probe diameter even for every measurement. Although both methods are elaborated both from the theoretical and practical point of view the final uncertainty of
the determination of mechanical properties using the AFM is rarely below 10%.
|
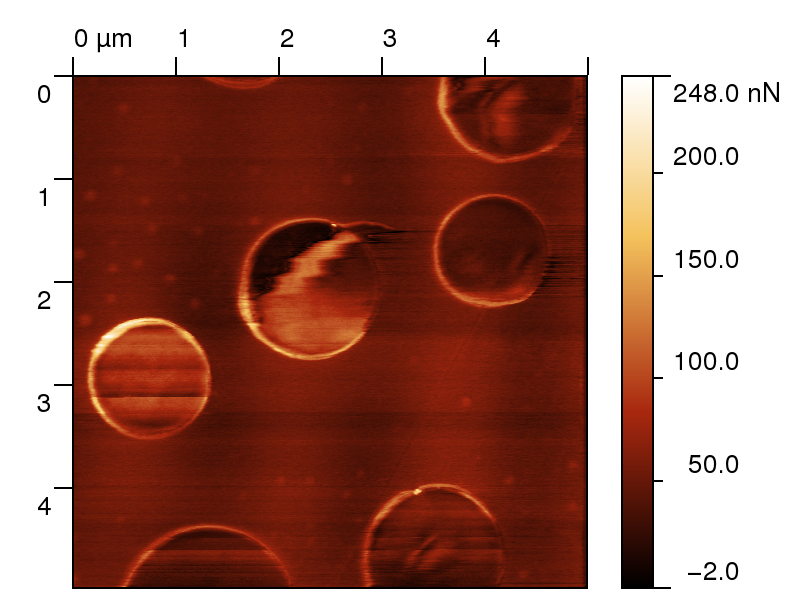 |
PeakForce QNM adhesion mapping |
Considering poor metrological properties of the AFM as a force converter other methods with much lower lateral resolution such
as nanoindentation and microindentation are used in nanometrology. In this case a diamond tip is pushed into the surface using a special device
featuring a most precise measurement of force and displacement that is possible. The resulting uncertainties can be therefore much smaller but of
course the lateral resolution is lost.
In the Department of Nanometrology in CMI we are dealing with the development of methods used for the data interpretation acquired during the measurement of mechanical properties using AFM, spring constant calibration of the probe holder (cantilever) offered as a service to the
customers and finally with the development of the traceability in mechanical testing using the nanoindentation and microindentation.
|