Scanning Thermal Microscopy
The scanning probe microscopy can be used even for the measurement of temperature, thermal conductivity and thermomechanical
properties. In this case the probe is much more complex however because it must work both as an interatomic force sensor and a temperature
sensor. There are basically three different practical designs:
- the probe consists of a thermistor made from two thin metal plates put on a standard AFM probe; we can measure the temperature,
- the probe is made from a single metal strip laid over the AFM tip; we can acquire the temperature (from the resistance of the strip) or
use the strip for local heating by running a current in the strip,
- the probe is formed by a thin shaped wire serving both as a probe holder (cantilever) and a probe itself. We can measure the temperature or
perform a local heating.
Nowadays more often are the resistive probes that enable also the local heating that can be used for thermal conductivity
measurements and for a thermomechanical properties analysis. During the measurement a bridge circuit is used which measures the probe resistance
(temperature) or it keeps the probe resistance constant while heating the probe (thermal conductivity).
In thermal conductivity measurements the probe is cooled down by the surface, so the system has to supply the corresponding
power in order to keep the probe temperature constant; it has to supply more power on a more thermally conductive material. The supplied power is
therefore the measure of the local thermal conductivity. However the relationship between these two quantities is not simple.
Generally the heat flow between the probe and the surface is a complex phenomenon where several mechanisms participate.
Such mechanisms can be a conduction between probe and the surface, a conduction of the adsorbed water layer, a conduction of the air around the
probe, a radiation of the probe or a cantilever conduction. The data analysis is therefore complicated in the case of a measurement of the thermal
conductivity as well as in the case of temperature measurements.
| 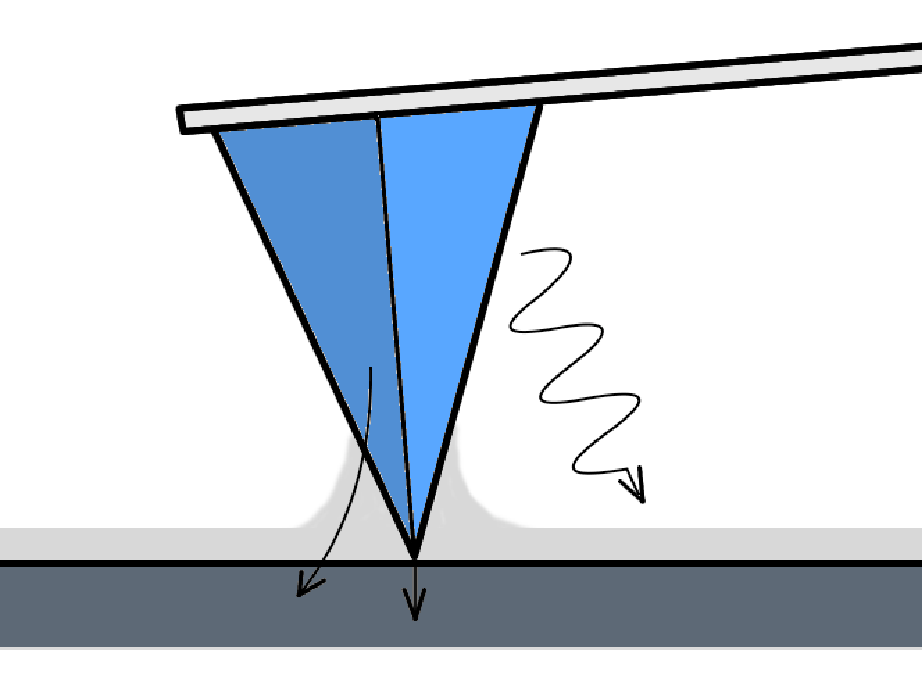 |
Mechanisms of the heat flow between the probe and the sample |
Another option constists in the variation of the probe temperature while observing mechanical changes - i.e. the reaction of the sample on the force applied by the probe. Such a local thermomechanical analysis can be used for the study of polymers because it is possible to
adjust the softening point of the polymer locally.
Quantitative measurement
The main problem of the Scanning Thermal Microscopy (SThM) technique is an unsufficient knowledge of the local geometry between
the probe and the surface, the influence of the adsorbed layer and therefore all the phenomena related to the heat transfer. The results of the
measurement are also influenced by the surface shape and its roughness. From the metrology point of view it is necessary to address the following
questions:
- analytical solutions and numerical modeling of heat transfer between the probe and the sample
- construction of probes with better geometrical parameters
- production of suitable reference materials
The most often approach for a quantitative analysis is based on the calibration of a particular probe (and the whole microscope)
on samples with known properties. This method does not take into account the surface geometry, changes of the probe shape and many other phenomena.
However this approach is often the only one possible as the whole process of the SThM signal formation is rather complex.
|